
The working element that separates material during this type of cutting is a focused laser beam. The operation principle is similar to plasma cutting technology: laser beam heats the material to a melting temperature, and then the melt is blown from the cutting zone via the gas jet under high pressure. There is another option of cutting waste removal, if sublimation laser cutting technology is used. In this case, a material is vaporized by laser existing momentum.
Laser cutting advantages
Laser cutting is usually used in cases when shortcomings and plasma cutting limits become critical in the manufacture of certain items - the former has a number of advantages.
-
Smaller bevel, less than 1°
Laser cutting technology provides substantially lower bevel compared to its plasma sibling, which guarantees more accurate values for the edges perpendicularity. When using default operating modes, it is possible to achieve smooth and straight cutting edges at the sheet thickness of 4 mm, while sheets of greater thicknesses possess edge bevel angle only about 0.5 °.
-
Less thermal effect
The laser beam is strongly focused and influences the metal in the narrow region of the cut only, which almost completely eliminates the effect of appearance of thermal deformations.
-
Absence of dross
Laser cutting technology generates very few dross on the edges of the sheet, making subsequent cleaning operations unnecessary, and allows one to transfer the workpiece immediately upon execution of the next process step.
-
Small kerf
Unlike the plasma cutting technology, the laser beam provides a very narrow and constant along the length kerf, whose width does not exceed 0.4 mm for any metal thickness. In its turn, the improved beam focusing increases the cutting precision, which is typically about ± 0.05 mm.
-
Better holes cutting
The minimum diameter of holes is approximately equal to the thickness of the metal in a continuous cutting mode. If the impulse mode is used, the machine is able to burn holes with a diameter 3 times smaller than the material thickness. The diameters of the holes cut by the laser beam at the bottom have a slightly larger diameter than the top, but perfectly round and of good quality.
-
High performance
For small sheet thickness (up to 6 mm) laser cutting speed is higher than that of plasma. However, it should be noted that the laser cutting speed drops significantly with further increase of the material thickness.
Laser cutting restrictions
At first glance it may seem that laser cutting is much more preferable to the plasma, but does not always hold and it also has its drawbacks.
Firstly, the cost for the laser cutting equipment is significantly higher that, of course, affect the operations price. Laser cutting is not cheap.
Secondly, the laser is effective for a small sheet thickness only - up to 6 mm, at most 20 mm. Not only because the cut speed significantly decreases significantly with growth of the sheet thickness. In addition, for thick materials power and gas consumption is very very high, that significantly increases the final cost of the product.
And third, the equipment for laser cutting is much more complicated, and therefore requires constant and skilled maintenance.
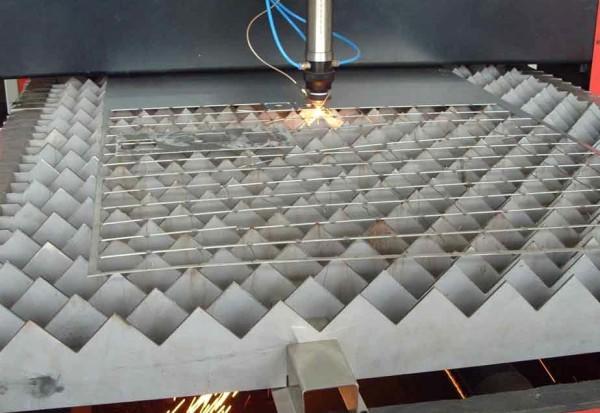
Laser cutting price
the rate in rubles per meter of cut
Mild steel
Thickness, mm | Cutting length up to 100 m | from 100 to 500 m | more than 500 m |
0.8 | 42 | 30 | 25 |
---|---|---|---|
1 | 47 | 31 | 26 |
1.5 | 50 | 36 | 30 |
2 | 52 | 42 | 35 |
2.5 | 57 | 49 | 43 |
3 | 67 | 56 | 50 |
4 | 77 | 65 | 56 |
5 | 92 | 76 | 66 |
6 | 112 | 92 | 75 |
8 | 162 | 117 | 95 |
10 | 207 | 182 | 134 |
12 | 255 | 212 | 168 |
16 | 460 | 340 | 310 |
20 | 560 | 505 | 460 |
Stainless steel
Thickness, mm | Cutting length up to 100 m | from 100 to 500 m | more than 500 m |
0.8 | 60 | 48 | 40 |
---|---|---|---|
1 | 60 | 53 | 44 |
1.5 | 98 | 68 | 52 |
2 | 125 | 88 | 75 |
3 | 165 | 135 | 95 |
4 | 220 | 165 | 125 |
5 | 320 | 220 | 155 |
6 | 420 | 310 | 230 |
8 | 620 | 460 | 360 |
10 | 760 | 610 | 460 |
Depending on the contour complexity, a correction coefficient can be applied, that may increase the resultant price from 1.1 to 1.5 times.